Crashworthiness of Carbon Fiber Composites
Test Instrumentation and Data Acquisition
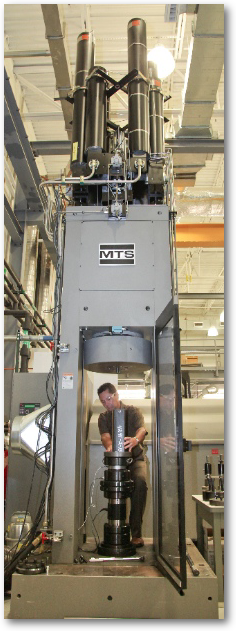
TMAC provides a unique capability to measure the specific energy absorption of crush tubes and other specimen geometries as a function of (constant) impact velocity within a range from quasi-static to 8 meters/second. Large scale specimens and structural components can also be tested in tension on the TMAC by adding a slack adapter and appropriate grips. Fixtures also exist for flat panel and beam type specimen geometries. User interest in this equipment remains very high with follow on projects and new projects being in the draft stage. Use of the machine is available for industry.
Custom-developed computer programs control and manipulate the test data from two high-speed data acquisition (DAQ) modules; a 12-bit synchronous card with four channels, and a 16-bit asynchronous card with eight channels. The program synchronizes the data and is triggered from the TMAC control software that initiates the impact. One card has higher signal resolution at the expense of temporal resolution and synchronicity, while the other card sacrifices signal resolution for fast, synchronous measurements. The functionality of the data system can be adjusted to specific test requirements, such as recording of multiple strain gage signals. The current DAQ configuration reads one Linear Variable Differential Transformer (LVDT) for displacement, a strain gauge based load cell and a piezoelectric load washer for force measurements, and two accelerometers. The accelerometers were chosen to provide 1-g/V sensitivity and 10-g/V sensitivity.
The accelerometer data are integrated to calculate the velocity, and this is being compared with the differentiated displacement data. The data for force, displacement, time, acceleration, and strain is synchronized with high-speed video for complete characterization of the crash. An air abatement system collects the carbon fiber dust cloud that forms during the crash.