Crashworthiness of Carbon Fiber Composites
Test Method
Advanced lightweight materials, such as polymer composites, aluminum, and high-strength steels, offer better crash energy absorption per unit of mass than do traditional materials. When those materials are tested to assess their response to crushing they exhibit different behaviors at different impact velocities. What happens in the transition zone between quasi-static impact rates (e.g., 2 inches per minute) and high-velocity impacts (over 10 mph) is not understood because the capability to conduct impact tests at intermediate velocities has been lacking. Test equipment installed in the Composites Lab at the Oak Ridge National Laboratory/National Transportation Research Center now fills that gap.
Typically, standard test machines are employed for experiments at quasi-static rates, whereas drop towers or impact sleds are the convention for dynamic rates. These two approaches bound a regime within which data for experiments at constant impact velocity are not available by conventional experimental practice. This regime is termed herein the intermediate-rate regime and is defined by impact velocities ranging from 1 m/s to 10 m/s. Investigation of rate effects within this regime requires experimental equipment that can supply a large force with constant velocity within these rates.
![]() |
Energy plot for crash test equipment.
|
TMAC
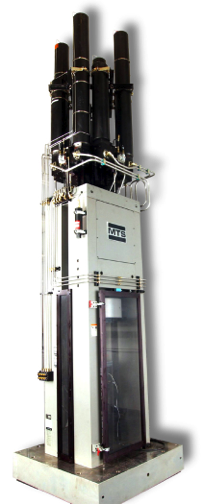
Using a drop tower or sled at intermediate rates, although technically possible, is problematic due to the prohibitively large mass required to maintain constant velocity during the crush. The Oak Ridge National Laboratory, Automotive Composites Consortium, and MTS Systems Corporation designed and built a servo-hydraulic crush test machine, Test Machine for Automotive Crashworthiness (TMAC) . Due to large available energy and the sophisticated simulation and control, TMAC can run high-force, progressive crush tests in the intermediate velocity range with prescribed velocity profiles.
Progressive Crash of Carbon Fiber Composite Tube