Spotweld Models for Advanced High Strength Steels
Executive Summary
This is a Phase II (technical feasibility) research project on development and implementation of a novel spot-weld modeling approach for structural analysis. The modeling is supported by the new spot-weld high-rate tests which will result in an interactive test database for various materials and spot-weld configurations. The developed methods will be used in advanced crashworthiness computer aided engineering (CAE) of spot-welded auto-body structures, and will enable more efficient design of structures for light-weighting while meeting crash requirement and cost-effectiveness. Phase I (concept feasibility) of the project successfully carried out the initial development of the Spot Weld Element (SWE) modeling framework and demonstrated of the effectiveness of such modeling approach.
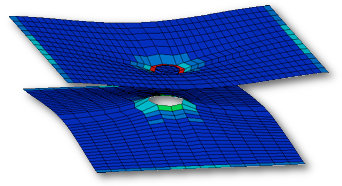
Main project tasks:
- Extend the applicability of Spot Weld Element (SWE) to various AHSS spot weld configurations and structural components.
- Extend SWE to multi-stack combinations of AHSS,
- Develop weld fracture criteria applicable to different loading and fracture modes, and different combination of materials,
- Develop a comprehensive impact testing database, and 5. Component level CAE model validation.
The objective is to develop the SWE based on microstructure-property model and implement it in FEM codes. The constitutive models will be based on strain-rate sensitive elasto-plastic fracture and damage mechanics, and the material microstructure. Welding process modeling will account for new materials and spot weld arrangements. The technology commercialization/industrialization plan is to have the SWE modeling framework developed in this project to be transferred and implemented into OEM advanced CAE crashworthiness simulation codes.